1 钻孔灌注桩施工技术措施
1.1钻孔灌注桩施工采用原浆护壁,正循环成孔施工工艺,水下浇筑混凝土成桩。施工过程严格遵照设计要求和执行《交通桥涵施工技术规范》的规定工艺和控制质量。
1.2材料检验:由材料组对每种进场材料进行材质检验,监督分包单位对材料复试。到场材料必须具有符合要求的合格证书,如对到场的材料有所怀疑,可停止使用。
1.3 成孔灌桩:
1.3.1 隔孔施工:在钻机就位之前,对埋设护筒的位置、深度和垂直度进行复查,以确保桩位准确。成孔时采用隔孔跳跃式流水操作,保证安全距离不小于4d,以防止对邻桩影响。
1.3.2确保桩身垂直成孔:垂直度是灌注桩顺利施工的重要条件,因此在钻架就位之后检查钻机平台平整和稳固情况,确保桩身成孔垂直度。
1.3.3控制钻进速度和护壁泥浆指标:控制钻杆钻进速度,应不大于1.00m/min,护壁泥浆相对密度控制在1.2~1.3左右。清孔时进行泥浆密度复验,相对密度控制在1.15~1.2左右。
1.3.4成孔检查:成孔之后对孔径、孔深和沉渣等检测指标进行复验,必须达到设计和施工规范要求后方可进行下道工序施工。
1.4 钢筋笼制作:钢筋笼的制作必须符合设计和施工规范要求。对钢筋笼的规格和外形尺寸进行检查,控制偏差在允许范围之内。下笼时监督施工人员对钢筋笼的焊接过程,必须按规范的搭接长度和标准焊缝进行操作,并按要求放置垫块,每节二组,每组三块,补足焊接部位箍筋。钢筋笼入孔后,将吊筋固定,避免灌混凝土时钢筋笼上拱。
1.5浇筑混凝土成桩:
1.5.1 工程采用C25混凝土,配合比由中心试验室设计。搅拌时由专职试验员负责控制混凝土配制工作,加料达到允许偏差范围之内。如遇雨天则对配合比相应调整。严格计量和测试管理,试块按要求制作,每根桩不得少于2组。
1.5.2 水下混凝土必须具有良好的和易性,控制坍落度在180~220mm之间。
1.53 混凝土灌注过程严格按照工艺规程进行,确保初灌量和控制导管埋入混凝土的深度不小于2米。灌注时导管不得左右移动,保证有次序地拔管和连续浇筑混凝土直到整桩完毕。工程桩的混凝土实际灌注高度比设计桩顶标高高出1米,以确保设计桩顶下桩身混凝土强度。
1.6冬季施工措施:
1.6.1降低混凝土水灰比。
1.6.2拌制混凝土的材料无冻结现象。
1.6.3混凝土拌制时间应适当延长。
1.6.4桩顶标高与自然地面标高相近的桩,其桩头应加草包进行保温。
1.7 质量保证措施:
1.7.1 建立以生产管理为核心的施工、技术、材料、安全和质量管理小组,开展质量教育工作,使每个职工都能树立良好的质量意识。每道工序严格把关,保证施工质量,以优质高效完成工程。
1.7.2 测量员要对轴线进行复核,以确保每根桩位置都符合设计要求,桩位正确。
1.7.3 质检员要对灌注桩施工的每一道工序认真进行复核,严格监督分包单位以设计要求和施工验收规范进行施工,做好隐蔽工程验收工作。
1.7.4 材料员要严格把好材料关。每批材料进场必须有质量保证书,并按规定进行复核,有权对不符质量要求的材料勒令退场。
1.7.5安保组要负责施工现场安全保卫工作及现场文明施工。
1.7.6试验员要严格掌握混凝土配合比的正确性,对材料情况监督,督促按规定做好试块及进行养护。
1.7.7生产管理组要全面负责生产的每一环节和每道工序的质量情况,组织好施工。
2 钻孔灌注桩施工
2.1施工技术
2.1.1测量定位和护筒埋设
2.1.1.1 测量定位:
2.1.1.1.1测量定位采用全站仪
2.1.1.1.2利用指定的轴线交点作控制点,采用极坐标法进行放样,桩位方向距离误差不小于5㎜;
2.1.1.1.3利用S3型水准仪来测定护筒标高其误差不大于1㎝
埋设护筒:护筒采用4㎜的钢板卷制而成,ф800工程桩护筒内径为Ф950,为防止钻进施工中护筒外圈返浆造成坍孔和护筒脱落,护筒埋入自然地面以下1~1.2米,进入原状土0.3~0.5米,护筒埋设位置应准确,其中心与桩位中心允许误差不大于20MM,并应保证护筒的垂直度和水平度。
2.2 成孔工艺
钻孔灌注桩全部采用正循环,三翼单腰带刮刀钻头回转钻进成孔,原土造浆护壁,正循环两次清孔工艺。吊车与导管灌注成桩(见工艺流程图)
2.2.1钻进参数:
2.2.1.1 根据桩孔施工地层特点及以往施工经验钻进技术参数为:压力10~30Kn;转速30~60R/min,泵量1500~1800L/min.
2.2.1.2 桩孔上部孔段钻进时轻压慢转,尽量减小桩孔超径。在易缩径的粘土层中,应适当增加扫孔次数,防止缩径。对‘硬土层’采用大压力慢转速钻进,以提高钻进效率。砂层中则用中等压力,慢转速并适当增加泵量。
2.2.1.3 上述方法通过实践证明是有效的,其优点虽回转阻力小,钻进较平稳,有一定的导向能力和钻进效率。
2.2.2桩孔质量检测;桩孔质量参数包括:孔径、孔深、钻孔垂直度和沉渣厚度。
2.2.2.1 孔深:钻孔前先用水准仪确定护筒标高,并以此为基点,按设计要求的孔底标高确定孔深,以钻具长度确定孔深,孔深偏差保证在正负30㎝以内。
2.2.2.2 沉渣厚度以第二次清孔后测定量为准。
2.2.2.3 孔径用孔径仪测量,若出现缩径现象应进行扫孔后,符合要求方可进行下道工序。
2.2.3 护壁与清渣:
2.2.3.1 泥浆性能指标:该工程泥浆采用原土自然造浆,泥浆性能指标如下表。
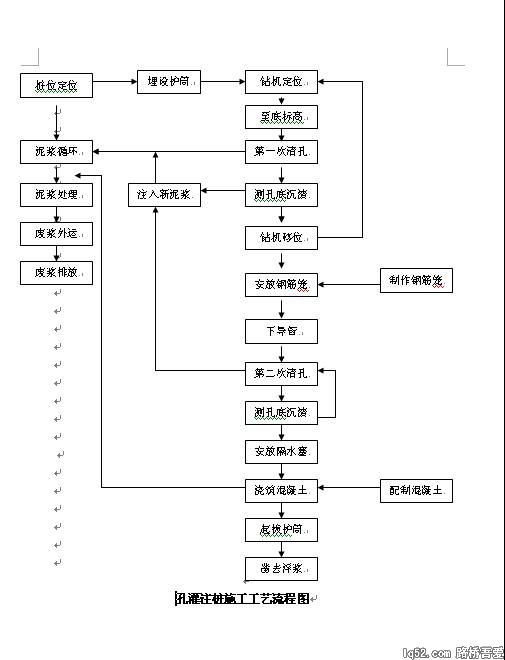
泥浆性能指标
层位 |
泥浆性能指标 | ||||
粘度 |
相对密度 |
相对
含砂量 |
胶体率 |
PH值 | |
亚粘土 |
18~20 |
1.10~1.18 |
|
96% |
7.5~8.0 |
粘土 |
19~21 |
1.15~1.25 |
<3% |
96% |
7.5~8.0 |
暗绿色粘土 |
20~23 |
1.15~1.25 |
<5% |
95% |
7.5~8.0 |
砂土层 |
19~21 |
1.18~1.30 |
<8% |
92% |
7.5~8.0 |
2.2.3.2 钻进粘土层中时,因原土自然造浆较强,泥浆返出时,孔口部位适当加入清水,防止泥浆稠化,增加钻进速度,但由于桩孔下部所要穿过的大部分为砂层,泥浆相对密度应控制在1.20~1.30之间,以便携带砂子,保证孔壁稳定。
钻进中应随时测定泥浆性能,确保注入泥浆性能指标。操作时要掌握好钻机起重钢丝绳与高压管的松紧度,减少晃动。加接钻杆前,应先将钻具提离孔底,待泥浆循环2~3MIN后再停泵加接钻杆。
2.2.4 清孔方法:
2.2.4.1 第一次清孔 桩孔成孔后,应进行第一次清孔,清孔时应将钻具提离孔底0.3~0.5m,缓慢回转,同时加大泵量,每隔10min停泵一次,将钻具提高3~5米来回串动几次,再开泵清孔,确保第一次清孔后孔内无泥块,相对密度达1.20左右。
2.2.4.2 第二次清孔 钢筋笼、导管下好后,要用导管进行第二次清孔,第二次清孔时间不少于30min,测定孔底沉渣小于10㎝时,方可停止清孔。
测定孔底沉渣,应用测锤测试,测绳读数一定要准确,用3~5孔必须校正一次。
清孔结束后,要尽快灌注混凝土,其间隔时间不能大于30MIN。第二次清孔注入浆相对密度为1.10左右,漏斗粘度18~25S,第二次清孔后泥浆相对密度控制在1.15左右不超过1.20。
2.25 泥浆的维护与管理:现场泥浆池体积每个150立方米,废浆池1000立方米,确保每天造孔钻进的需要。泥浆池及循环系统,主泥浆循环槽规格为0.5×0.6m,成孔过程中,泥浆循环系统应定期清理,确保文明施工,泥浆池实行专人管理、负责。对泥浆循环和沉演池的渣土(砂性土),专门配备一台抓斗机进行打捞,处理后的渣土经数次翻晒后作干土外运。
2.3钢筋笼的制作与吊放
2.3.1钢筋笼按设计图纸制作,主筋采用单面焊接,搭接长度大于等于10d。
2.3.2加强筋与主筋点焊要牢固,制作钢筋笼时在同一截面上搭焊接头根数不得多于主筋总根数的50%。
2.3.3 发现弯曲、变形钢筋要作调直处理,钢筋头部弯曲要校直。制作钢筋笼时应用控制工具标定主筋间距,以便在孔口搭焊时保持钢筋垂直,防止提升导管时带动钢筋笼,严禁弯曲或变形的钢筋笼下入孔内。
2.3.4钢筋笼在运输吊放过程中严禁高起高落,以防弯曲、扭曲变形。
2.3.5每节钢筋笼用焊3~4组钢筋护壁环,每组四只,以保证混凝土保护层均匀。
2.3.6钢筋笼吊放采用活吊筋,一端固定在钢筋笼上,一端用钢管固定于孔口。
吊筋长度计算如下:L=L1-L2+S
式中L---吊筋长度
L1护筒的绝对标高;
L2钢筋笼顶绝对标高
S护筒上口至固定钢管的距离。
由于使用的钢筋不同,焊条应根据母材的材质合理选用。
2.3.7 钢筋笼入孔时,应对准孔位徐徐轻放,避免碰撞孔壁。下笼过程中如遇阻,不得强行下入,应查明原因处理后继续下笼。
2.3.8每节钢筋笼焊接完毕后应补足接头部位的箍筋,方可继续下笼。
2.3.9钢筋笼吊筋固定以使钢筋笼定位,避免浇筑混凝土时钢筋笼上浮。
2.4 混凝土的浇筑
2.4.1原材料及配合比
2.4.1.1 水泥应符合规范要求,采用P·O32.5水泥并经过试验合格,严禁使用快硬型水泥,水泥必须有出厂合格证书,如果水泥出厂日期超过三个月对水泥质量有怀疑时应视不同情况进行复验,复验合格后方可使用。水泥在运输及堆放过程中应有防雨、防潮措施,不同品种、标号、生产厂家的水泥严禁使用在同一根桩混凝土中并应分别堆放。
2.4.1.2石子的质量应符合规范要求,每批石料进场应验收合格方可入场。碎石的料径采用5~31.5㎜,泥含量不得大于1%,针片状含量不超过15%,压碎值不超过12%。
2.4.1.3 砂的质量应符合规范要求,选用级配合理、质地坚硬、颗粒洁净的中粗砂,砂进场每批需验收合格,细度模数控制在2.3~3.0之间,在储运堆放过程中防止混入杂物。
2.4.1.4 外加剂应符合规范要求并有质保书,确认合格后,方可使用。
2.4.1.5配合比由公司中心试验室提供,严格按配合比称量,不得随意更改。
2.4.2混凝土搅拌
施工现场设混凝土搅拌站,由JZC-350型搅拌机、砂石堆场和水泥库组成。混凝土搅拌时应严格按配合比称量砂、石、外加剂。混凝土原材料投量允许偏差:水泥、水、外加剂为±1%;砂、石±2%。原材料投料时应依次加入石、砂、水泥和外加剂,混凝土搅拌时间不小于90S。混凝土搅拌过程中及时测试坍落度和制作试块,拌好的混凝土应及时浇筑,发现离析现象应重新搅拌,混凝土应及时浇筑,发现离析现象应重新搅拌,混凝土坍落度控制在18~22㎝。
2.4.3混凝土浇筑
2.4.3.1 浇筑采用导管法,导管下至距孔底0.5m处,导管使用25㎝规格。导管使用前需进行通球和压水试验,确保无漏水、渗水时方能使用,导管接头连接处须加密封圈并上紧丝扣。
2.4.3.2 导管隔水塞采用水泥塞,塞上钉有胶皮垫,其直径为大于导管内径20~30㎜。为确保隔水塞顺利排出先加0.3M砂浆,剪球后不准再将导管下放孔底。
2.4.3.3 初浇量要保证导管在混凝土中0.8~1.3m。本工程混凝土初浇量不得小于1.8立方米。
2.4.3.4 浇筑混凝土过程中提升导管时,由各机配备的质检员测量混凝土的液面高度并做好记录,严禁将导管提离混凝土面,导管深度控制在3~8M,不得小于2M。
2.4.3.5 按规范要求制作试块,试块为150×150×150㎜,每根工程桩做二组试块,脱模后放入标养室养护,28天后进行试验。
2.4.3.6 灌注接近桩顶标高时,应严格控制计算最后一次混凝土量,使桩顶标高比设计标高高1.0米左右。
2.4.3.7 混凝土浇筑过程中应防止钢筋笼上浮,混凝土面接近钢筋笼底部时导管埋深宜保持3米左右,并适当放慢浇筑速度,当混凝土面进入钢筋笼底端1~2米时可适当提升导管,提升时要平稳避免出料冲击过大或钩带钢筋笼。
3.保证措施
3.1管理措施
3.1.1公司的工程技术部直接对该项目的工程质量进行监督与控制,直接掌握工程质量动态,指导全面质量管理工作,开展严格岗位责任制,对各工序、工种实行检查监督管理,行使质量否决权。
3.1.2对主要工序设置管理点,严格按工序质量控制体系和工序控制点要求进行运转。
3.1.3实行三级质量验收制度:每道工序班组100%自检;质检员100%检验;工地技术负责30%抽检。
3.1.4认真填写施工日记。
3.2 技术措施
3.2.1 轴线及桩位放样,定位后要进行复测,定位精度误差不超过5㎜。埋设护筒时由测量人员到场,用经纬仪纠正中心后方能固定护筒,保证护筒的垂直度。
3.2.2 钻机定位、安装必须水平,现场配备水平尺,当钻进孔深达到5M左右时,用水平尺再次校核机架水平度,不合要求时随时纠正。
3.2.3在第一次清孔时,钻机稍离孔底进行往返数次扫孔,把泥块打碎,检测孔底沉渣小于10㎝方能提钻。钢筋笼在孔口焊接时,运用十字架吊锤法,确保整体钢筋笼的垂直度。
3.2.4混凝土搅拌时砂石料经过磅秤称量,误差不超过2%。严格控制水灰比。根据现场砂石料的含水情况调整加水量。每根桩做1~2次坍落度检验。
3.2.5 混凝土浇筑严禁中途中断,提升导管要保证导管埋入混凝土中3~8米。
3.2.6 根据地层特点及时调整泥浆性能,防止钻孔缩径和坍孔,进入砂层时泥浆相对密度必须控制在1.15~1.25之间粘度20~25S确保孔 壁稳定。
4 施工重点
4.1清孔
在我们接触过的工程中,大部分人只用一次清孔,往往造成一根桩需清孔一天多时间,假如用二次清孔可以节省一半时间,且在浇筑前沉渣厚度容易控制,采用一次清孔往往造成等钢筋笼、导管下完后,再测孔深时发觉孔深又差了很多;
4.2 孔规
我们大多工地不用孔规,认为没必要,而且浪费。我就拿宁通公路一个工程来说明一下,1995年我们在在宁通公路施工,开始的第三根桩钢筋笼下到近30米时,钢筋笼怎么也下不去,各种方法想尽、用尽也没有把钢筋笼下去,最后只有把钢筋笼提起一节一节重新割断,再下钻杆在30米处来回扫孔,最后才把钢筋笼放下去,这根桩比其它桩多用了三天时间,假如先用孔规下去检验一下不就没有这些麻烦了吗?
4.3 混凝土
我认为浇灌注桩的混凝土和易性要好,且石子是连续粒级,但在大部分工地上我见到是用20~40㎜的单粒级石子,有些工地认为这样省钱,其实这样并不省钱,如在宁通公路某桥的一根灌注桩由于是单粒级石子,混凝土发生了离析,造成堵管,这根桩处理共花费近十几万元,这样省钱吗?